Plastic Molds are used to produce a variety of products. The products made range from computers, soda bottles and toys to car parts, storage bins and kayaks. This is a very efficient process and produces little waste.
It also has the advantage of reducing inventory and carrying costs. This helps to improve ROI. Contact American Plastic Molds now!
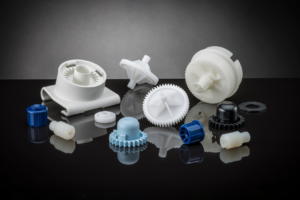
The cost of plastic molds varies depending on the complexity of the part that needs to be created. Generally, it takes six to twelve weeks to build a new plastic mold, which is expensive and time-consuming. However, a well-designed plastic mold can reduce the overall production costs of your product by eliminating the need for costly reworking and redesigning of the part.
Injection molding is a common manufacturing technique that produces plastic parts at high volumes. It is ideal for manufacturing items that require repeatable processes such as wire spools, bottles, bottle caps, toys, combs and musical instruments. Injection molding is also an environmentally friendly process, requiring less energy and fewer resources than traditional manufacturing methods.
When designing a plastic mold, it is important to consider the product’s purpose and how many units will need to be made. Smaller molds are often cheaper than larger ones. The type of plastic you use also affects the price. High-performance plastics, such as polycarbonate and ABS, are more expensive than standard grades. Also, adding features like heated runners and sprues can increase the upfront cost. However, these components can also help to reduce material waste and cycle times, which can result in significant savings in the long run.
It is essential to understand the basics of injection molding before getting quotes from different suppliers. Detailed drawings and prototypes are required to properly estimate the initial costs. Using these documents can help you make informed decisions about the type of mold that is best for your project. In addition, you should always be clear about the intended production volume and timeline before committing to an injection mold.
Choosing the right plastic mold is crucial for a successful project. A well-designed plastic mould can save you money in the long run by reducing the number of costly reworking and redesigns required for a perfect finish. It is also important to choose a plastic material that will meet your specific requirements. For instance, if your project involves a lot of mechanical stress, you should look for a stronger and more durable material such as steel or aluminum.
Flexibility
Injection molding is a versatile process that accommodates a wide range of thermoplastic and thermosetting plastic materials. These materials provide a high level of design flexibility and aesthetics while minimizing production costs, weight and waste. The flexibility of injection molds allows manufacturers to produce complex parts with tight tolerances, allowing them to meet the needs of demanding customers.
The process of producing plastic injection molds involves pouring a liquid or powdered polymer into a hollow mold and then exposing it to heat and pressure to form the desired shape. Injection molding is often used for making replacement parts for metal products, such as car bumpers or bicycle handles. However, it is also used to make many other types of products, including packaging and consumer goods.
One of the most important aspects of a successful injection mold is the quality of the raw material used to make it. The material must be heat-resistant and able to withstand high temperatures. In addition, it must have good tensile strength and toughness to withstand the stresses of use.
Another important factor is the thickness of the raw material, which should be consistent throughout the product to prevent shrinking or distortion. The thickness of the raw material is determined by the type of plastic and the desired product’s physical characteristics.
Injection molds require regular maintenance to ensure optimum performance and service life. This includes cleaning, inspection and repair of the mold, as well as proper handling to avoid damage from ejector pins or manual wiping with sprue pliers. It is also important to prevent rust, which can occur due to water leaks or condensation.
The plastic injection mold is a complex system consisting of several parts, each with its own purpose and function. These include the pouring system, temperature regulating system and molding parts. The pouring system and molding parts are in direct contact with the plastic and are subject to the most frequent changes. Injection molding companies also offer a range of options for customizing and improving plastic molds. For example, they can add a cooling channel to reduce warping and shrinkage in the finished product.
Durability
The durability of plastic molds depends on a number of factors, including the type of plastic used, working conditions, and maintenance procedures. For example, high-viscosity materials may require more pressure to inject into the mold, resulting in faster wear and tear. In addition, impurities in the molten plastic can also affect the mold’s structural integrity and appearance. The design of the injection molding machine and mold structure also play a role in plastic mold durability. These factors include draft angles, surface finish, and undercuts. A well-designed plastic mold will be easy to demold, reducing overall production costs.
There are many types of plastic molds, each with unique properties for specific applications. Silicone molds are flexible and are ideal for prototyping, while metal options like aluminum and P20 steel are preferred for high-precision projects. Other options are available, such as pre-hardened or corrosion-resistant steels, which offer better cutting, machining, and polishing properties. Stainless steel is a popular choice for chemically resistant products, and can be refurbished several times.
Injection molding machines and molds must be durable enough to withstand the intense stress of repeated use, particularly when producing abrasive or reinforced plastics. Suitable cleaning and lubrication help preserve the plastic mold’s condition and extend its lifespan. In addition, routine maintenance and inspection for damage are critical to preventing premature failure.
Injection molds are designed for a certain number of cycles, and the lifetime can vary depending on the type of plastic and the operating environment. Some types of plastic are more abrasive than others, and high-volume or rapid production speeds can accelerate the degradation of the mold. Fortunately, there are many ways to improve the durability of plastic injection molds, such as selecting high-quality repair materials and ensuring that all parts are made in the same temperature conditions. This helps prevent thermal fatigue, which can lead to dimensional changes in the finished part and mold. In addition, a proper gating system and temperature control ensures even distribution of molten plastic across the cavity, minimizing heat stress. In addition, proper handling and storage of the injection mold will help protect it from contamination and abrasion.
Environmental Impact
The use of plastic injection molds poses several environmental challenges. These issues range from the depletion of natural resources to the accumulation of waste in landfills and oceans. Sustainable practices are essential to mitigate these issues. Eco-friendly plastics and greener injection molding processes offer promising solutions to these concerns. Policy changes and industry shifts can also promote these solutions.
The process of producing plastic injection moulds consumes a lot of energy, requiring significant heat and electricity to melt and form the materials used. This high energy consumption increases production costs and contributes to greenhouse gas emissions. Efforts to reduce these emissions should focus on reducing the amount of energy consumed and exploring alternative sources of power. The resulting savings can be used to improve manufacturing efficiency and increase productivity.
Plastic injection molding is a major contributor to climate change, with its processes causing CO2 and other greenhouse gases to build up in the atmosphere. These gases trap heat and cause the Earth to warm, which in turn leads to more extreme weather events like heatwaves, droughts, floods, and hurricanes. They can also result in polar ice caps melting, which decreases the planet’s reflectivity and contributes to further warming.
Moreover, plastic injection moulds can also leach harmful chemicals into the environment. These toxic substances can contaminate soil and water systems, and pose serious health risks to marine life and humans. These chemicals are known as persistent organic pollutants (POPs), and include bisphenol A (BPA) and phthalates, which have endocrine-disrupting properties. Moreover, they are resistant to degradation and can remain in ecosystems for extended periods of time.
The durability of plastics may be an advantage when it comes to product lifespan, but this durability poses a challenge in terms of end-of-life management. Because most plastics are not designed for recyclability, they end up in landfills or contribute to the growing problem of environmental pollution. The recyclability of plastics can be improved by increasing recycling rates and promoting environmentally friendly waste management policies. In addition, efforts to develop biodegradable plastics can help reduce the burden of traditional plastics on the environment.